A lot of techs and companies like to put their best foot forward and try to convince you that they are perfect all the time, but I have built this company under a different kind of vision…. honesty. I would rather talk about how I overcame a difficult situation than try to convince you that nothing ever goes wrong with a repair. In this case a MacBook Keyboard repair that for some reason everything went wrong!
The repair
If you have been paying attention to the Mac World you would know that there was a few years were Apple had a hard time with MacBook Keyboards. They mostly work fine but there are a small group of MacBooks that the keys stop working or just fall out. Apple even had an extended “Repair Program” for this problem and would repair the MacBooks for free. But that particular repair program has ended.
What makes this repair difficult is that the only way to Perform this MacBook Keyboard repair to remove every part of the MacBook from the Top case and move it to a new top case. (Basically the MacBook is build into a keyboard….. Kind of makes sense if you think about it)
My Client has a 2017 15″ MacBook Pro that just happens to have issues with its keyboard. Knowing that this was going to be a tough repair (And not cheap) I suggested that the client use an external Keyboard. However the client mentioned that the way they use their MacBook an external keyboard was not going to help. (Very reasonable answer) even after telling them how much it would cost they considered it a good idea to go ahead with the repair (Also very reasonable)
I have done many repairs just like this what could go wrong?
I knew this was going to be a tough repair when the part arrived. Just looking at the part I could tell it was not going to work. Mostly having to do with the part was for a 13″ MacBook keyboard repair .,… not the 15″. I double checked the model number of my order. Double checked the model number on the actual MacBook and also checked the part number on the box that came with the part. Sure enough everything was correct except for the part inside the box. My supplier was very quick to fix the issue and sent me the correct part ASAP. (One of the reasons why I use them is quality of parts and when there is a problem they fix it without causing trouble)
This unfortunately meant that I needed to call the customer to let them know about the delay. . . .and they live in an area with no reception and no internet. (Got to love regional Australia sometimes). So all I could do is document the issue and call get to work the moment the part arrives.
Stripped screws on the Wifi ANTENNA
So when I say stripped screws most of you who have ever tried do a repair on any other device would think that is an easy fix just use pliers to remove the screw.. Except that this is a MacBook keyboard repair. The screws are TINY. to give you an idea of how tiny the screw is look at the Botton of your iPhone near the charge port…. You know those two tiny screws you never noticed before. THOSE are the size of the screws. and I had 5 out of the 14 needed to remove the second most expensive part on the MacBook stripped.
Yep that is right. I needed to remove these screws in order to remove the wifi antenna so I can remove the MacBook Retina Display. In the 15 years of doing MacBook Repairs I have never had this problem.
Now with normal striped screws you can be a little rough with the screw in hopes that it comes out. For a MacBook Keyboard repair I have to be extremely careful. If
I crack that display the cost for me to replace it is about $500 (My cost … not the customers). So what do I do … Visit Bunnings.
I needed to purchase a Dremel. For you folks that are not into tools this is a precision rotary tool that is similar to a dentist drill. They are often used for engraving but I am going to use this to drill out these tiny screws.
When I was at Bunnings I noted that the Dremel did not come with the right size drill bit. So when asking for help the poor salesperson kept brining me tiny screws just to have me say “That is way too large … got anything smaller” . I ended up needing to order the part online… yet another delay.
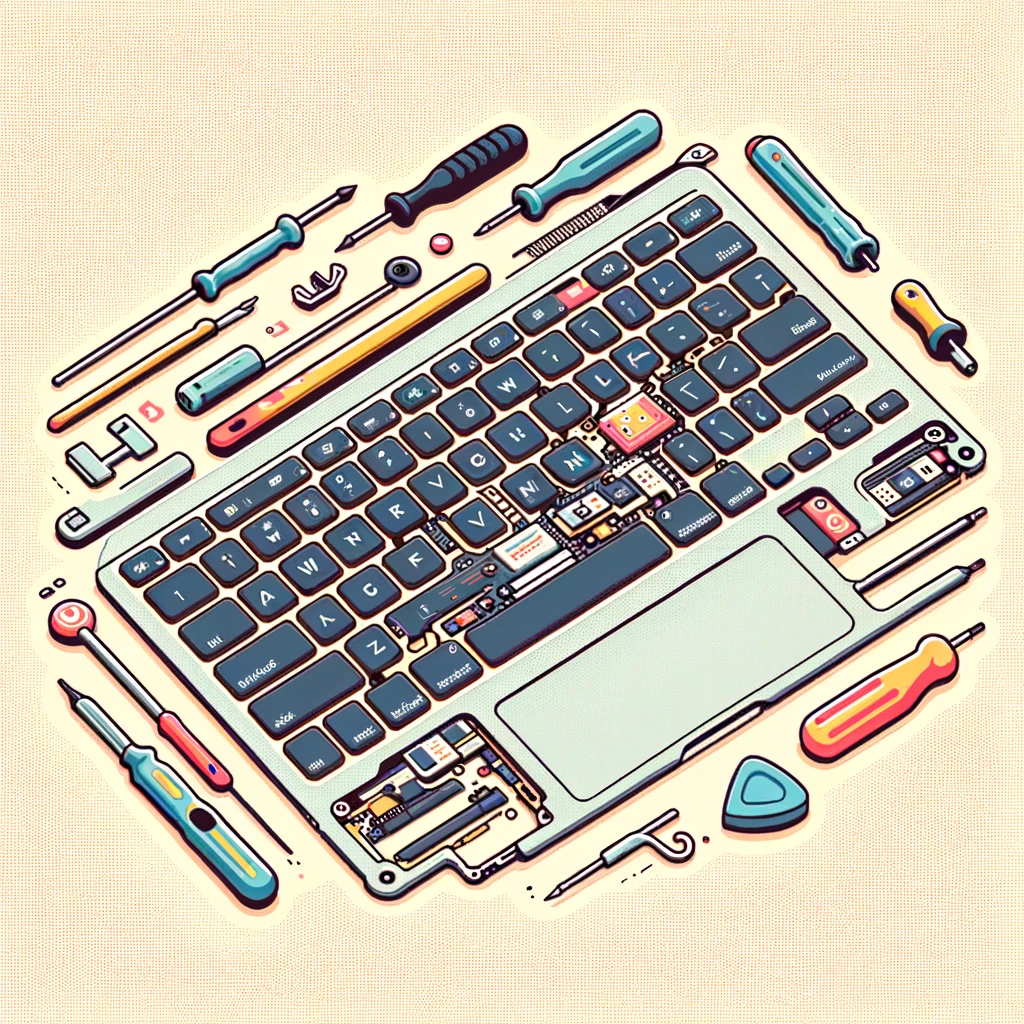
EMERGENCY Room visit
Yep you read that correctly. Just as I started to work on the MacBook I got a call from my wife that she had an accident while working on the house renovation and the ambulance was on its way. I put down the repair and ran home (My wife had the car)…. 1.8 Kilometres later I arrived just as the paramedics finished loading her into the car.. they waited long enough to see if I was going to have a hart attack and took her to the hospital (I need to start jogging)
While this only resulted in 15 stitches on her leg.. she was told to keep her leg up in the air and I needed to stay home to take care of her. This also meant that no sleep, limited hours … I was not going to be able to do that repair… anytime soon.
Steady hand Required
On my first day back I put this MacBook at my top priority. The customer had been very patent. The problem was that the nature of drilling out screws on a MacBook requires very steady hands. And with my current state I was just not able to do that. See unlike a car or heavy machinery where a slip of a took can cause a little trouble there is little chance you can cause any real harm to what you are repairing. On a MacBook even the shavings from the Dremel can destroy the computer. So a slip of the drill bit is enough to make this a very expensive repair for me (Not the customer)
Once I had removed the screws I was extremely careful to make sure there were no shavings of any kind left in the MacBook. (Nylon brushes, Bellows to blow out shavings and an ESD compliant vacuums. )
Too much stubborn glue
What a lot of people do not know about MacBook Keyboard repairs is there is a lot of parts that are glued into the MacBook, Including the battery., speakers and many of the ribbon cables. The issue with this is that Apple uses some amazing glue. Solvents and heat are the best way to remove these parts from the MacBook .. they just happen to be the best way to harm the parts as well. This means it is a slow process.
Too much heat and the part is damaged. too little and I can damage the part while trying to remove it…. Speaking with experience here.
At this time what I needed to do is take my time to make sure that this did not go wrong. It’s better to tell someone that you are taking your time because you take pride in your work than to rush a repair .. no matter how angry the customer may be. Lucky for me the client was very patient.
Time for testing …just to be sure
One of the things to consider when performing a MacBook Keyboard Repair is that you are removing almost every single part out of the computer. This means there is a large chance of something not connecting the way it should. There is also a chance that something that was working before the repair is not working now, mostly do to a cable not fitting correctly. The only problem with this is the only way to find out is to have the device put together and test it.
Sure enough I got the device working but one thing was not working. The Keyboard. At this point I was exhausted, frustrated and it was 4:45. I told my staff to close the doors sharply at 5:00 because I really needed to focus on this repair.. Then I thought better of it.. instead of taking the system apart and starting over when I was tired I figured it was a better idea to get some rest come in early and do the repair then.
Three hours before Opening
Sometimes you just need to walk away from a repair, clear your head, and come back. While many Computer techs like to sink their teeth into a repair like a pit bull and keep working until it is finished , I have learned that it is a good idea to stop, clear your head and come back to the repair when you are thinking correctly.
Sure enough this was the right idea. Because I was able to find the problem with the repair. One of the cables when the Logic Board was put back into the top case had slipped. This meant that I did not have to completely take apart the MacBook.
And just to be sure I give this computer a very through run through including loading one of my known good versions of the OS.
Ending the repair like it should with a Apple Logo
There is something that makes a tech smile like seeing the Apple Logo appear when you have been working on a Mac for so long. While this is does not mean that everything is working ok .. it is a good start.